Mass customisation could not be possible without the utilisation of machinery as a tool to mass produce prefabricated building elements. Using Rotheroes diagram of automated making; from the virtual representation of an object to the labour and fabricated artifact itself, it can be seen how conventionally 3D printed objects follow a strict, linear method of toolpath generation from an .stl file that sends an instructional g-code file resulting in a 3D printed artifact:
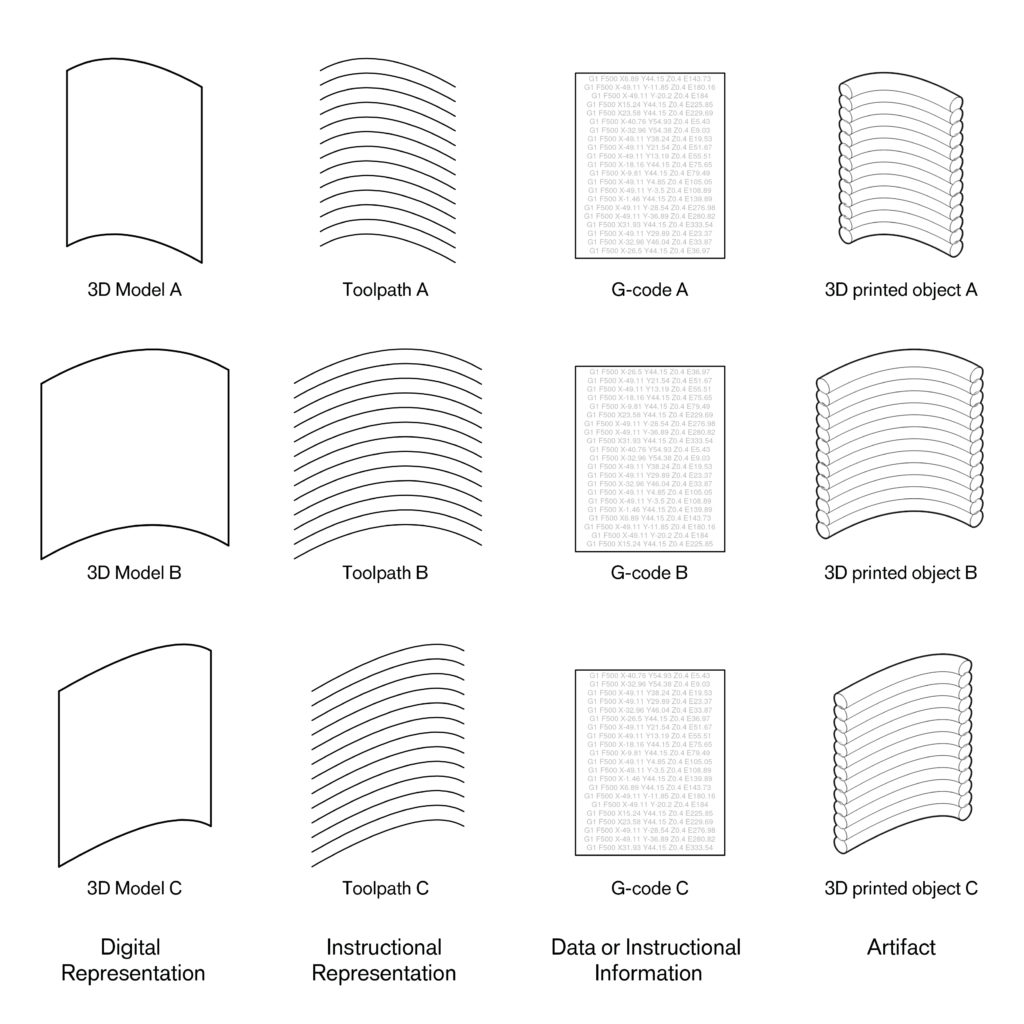
This would mean fabricating multiple unique objects would require multiple unique 3D model inputs. However, through experimenting with manipulating toolpath and G-code generation, multiple custom-crafted printed objects can be achieved with a single 3D model:
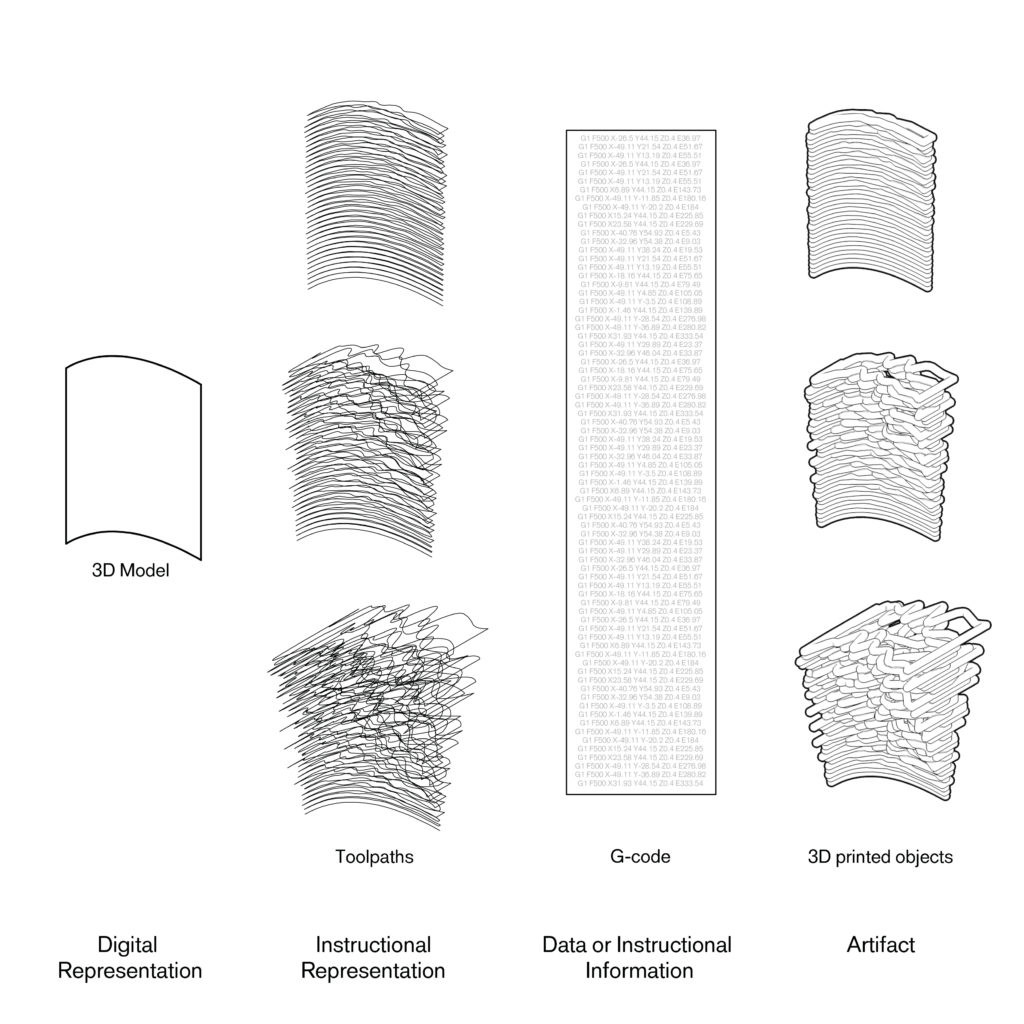
To apply these explorations to a mass scale, it was necessary to automate the process. This was achieved by accessing the control points of a contoured toolpath, essentially the DNA of a 3D print:
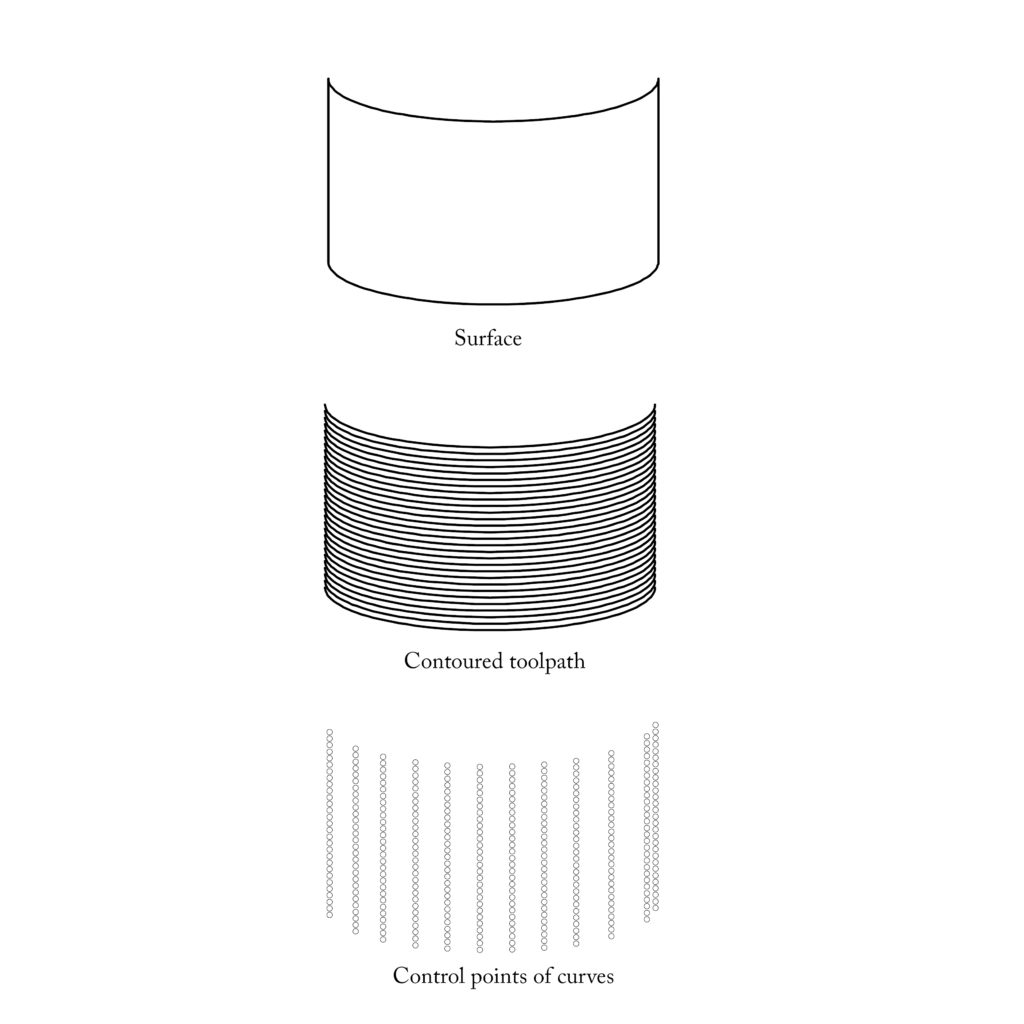
By jittering the control points of the contour curves and rebuilding the curves, one-of-a-kind toolpaths were introduced despite having the same 3D modelled surface input:
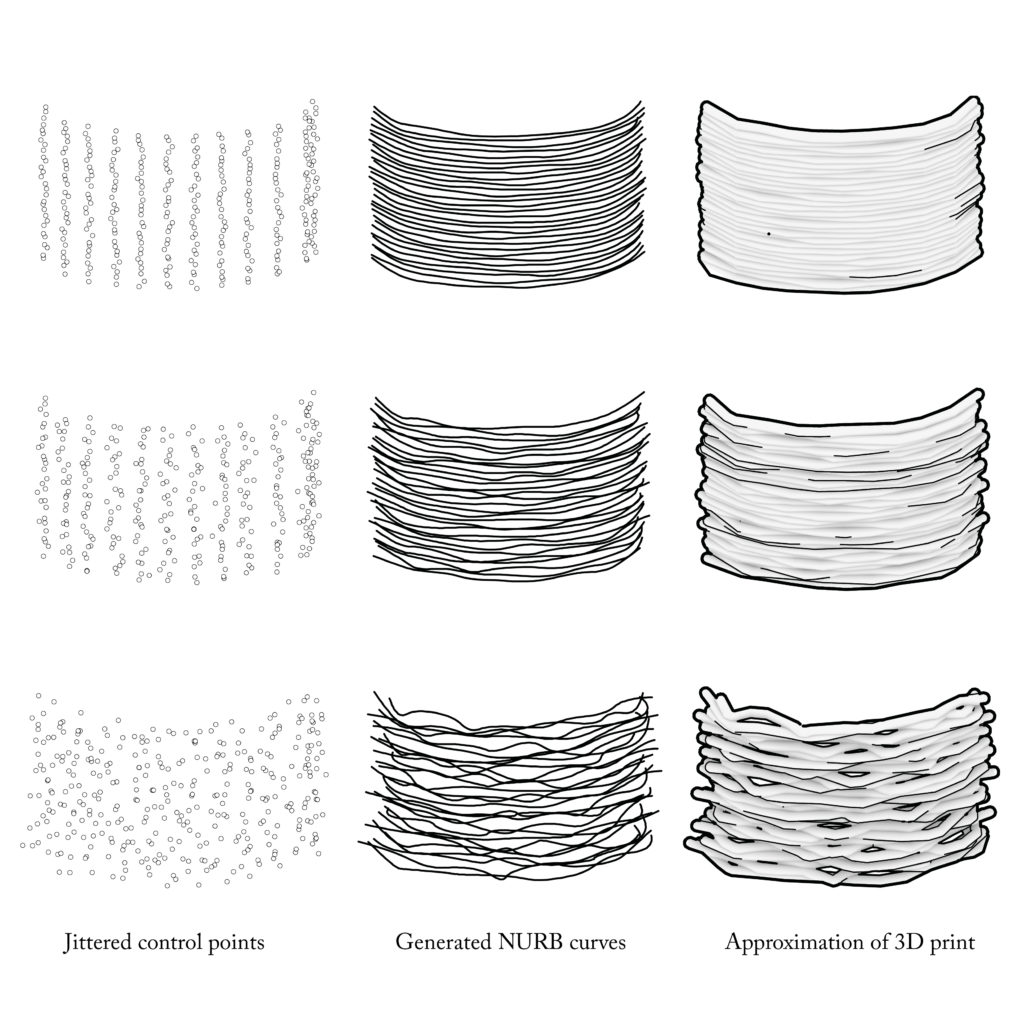
As the whole process from modelling a surface to generating a toolpath was automated, more focus was spent on designing the parameters of the jittering itself.
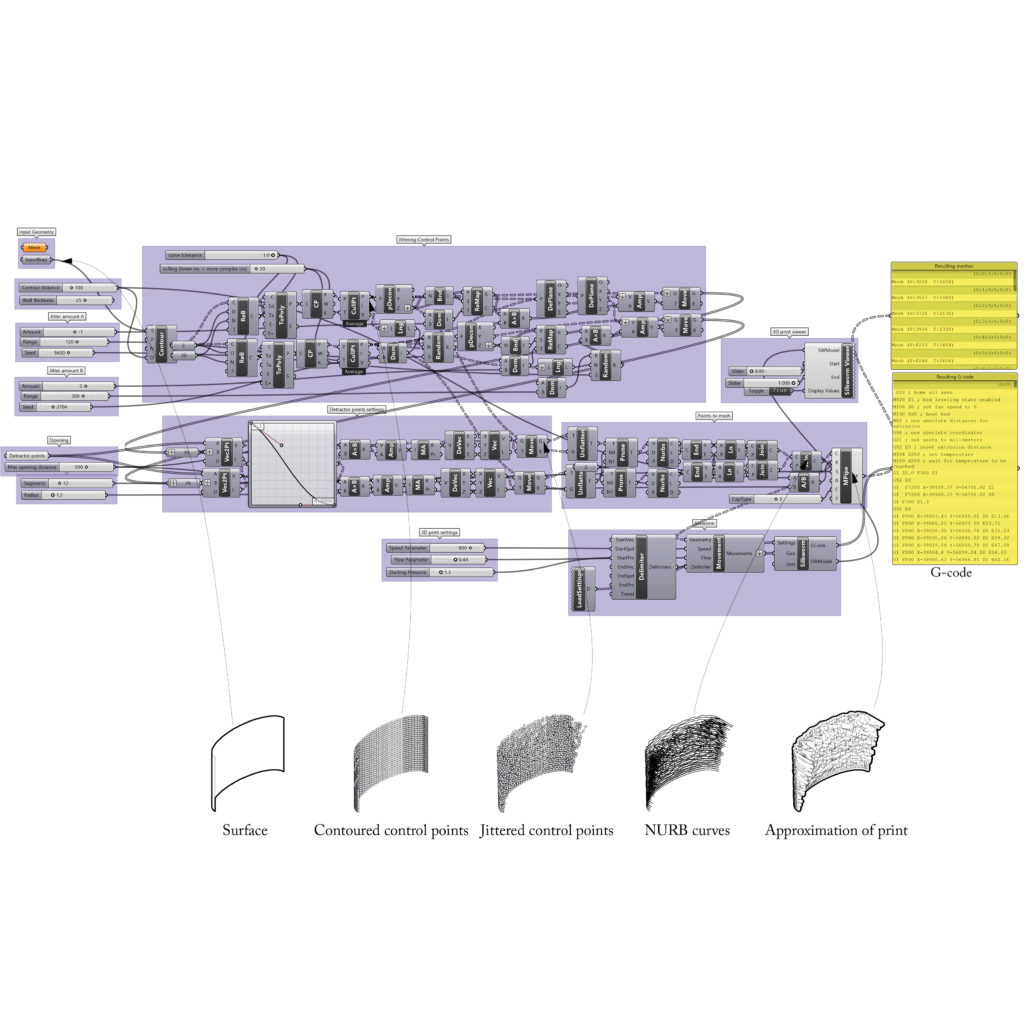