Material and Computation
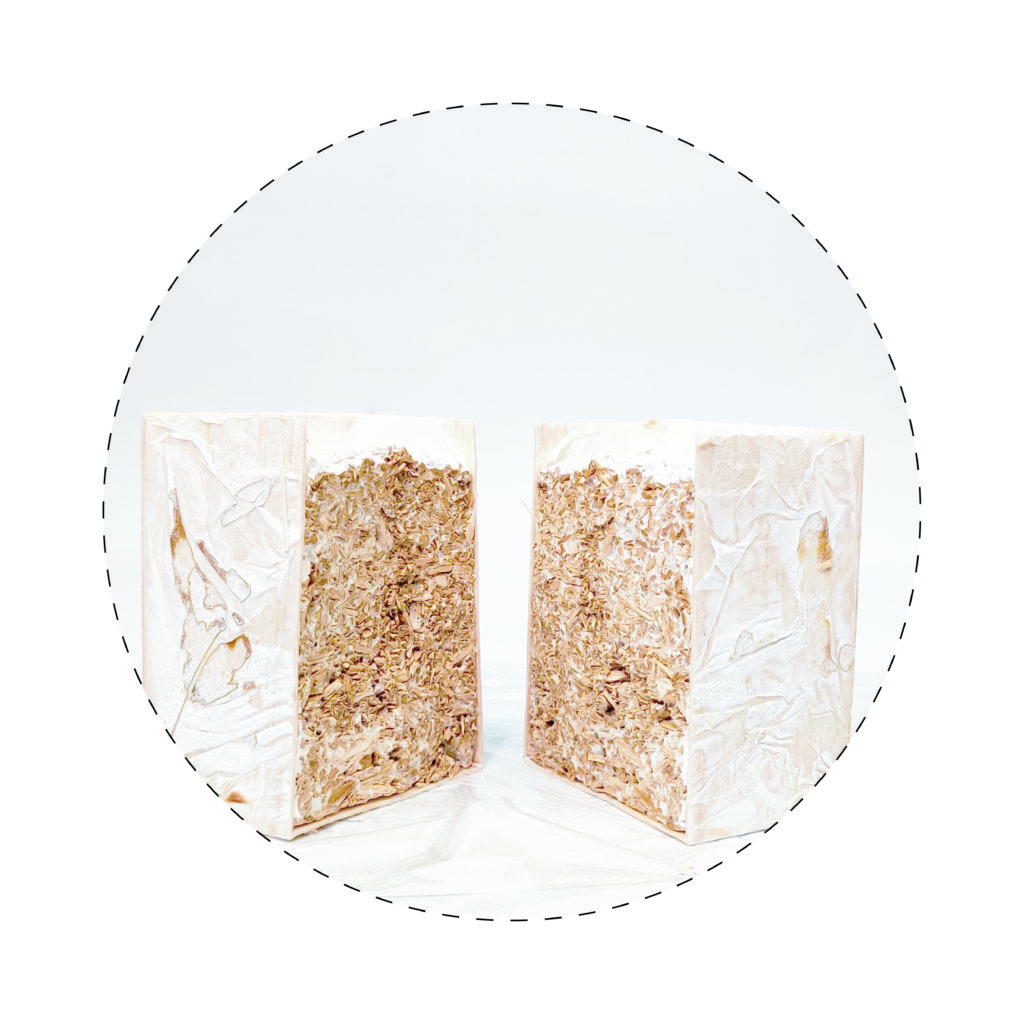
As a living organism, it needs oxygen to grow
Regardless the substrate, 10 to 15 cm growth in depth was observed
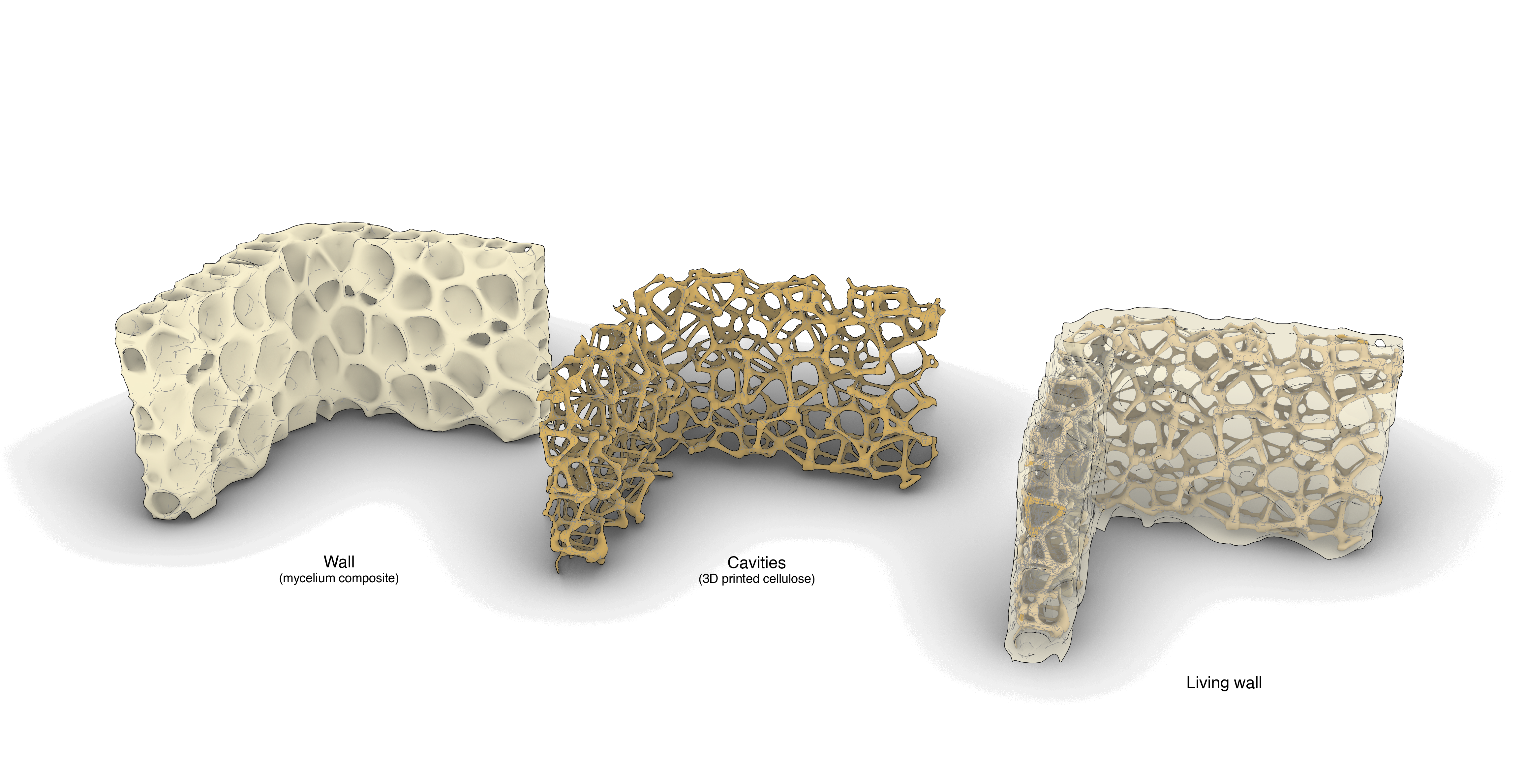
Decreasing the volume by 40%
Weight per cubic meter of composite with wood-chips is 20% of CLT
Optimised geometry and condition for the mycelium composite is derived through computational design supported by experimental findings.
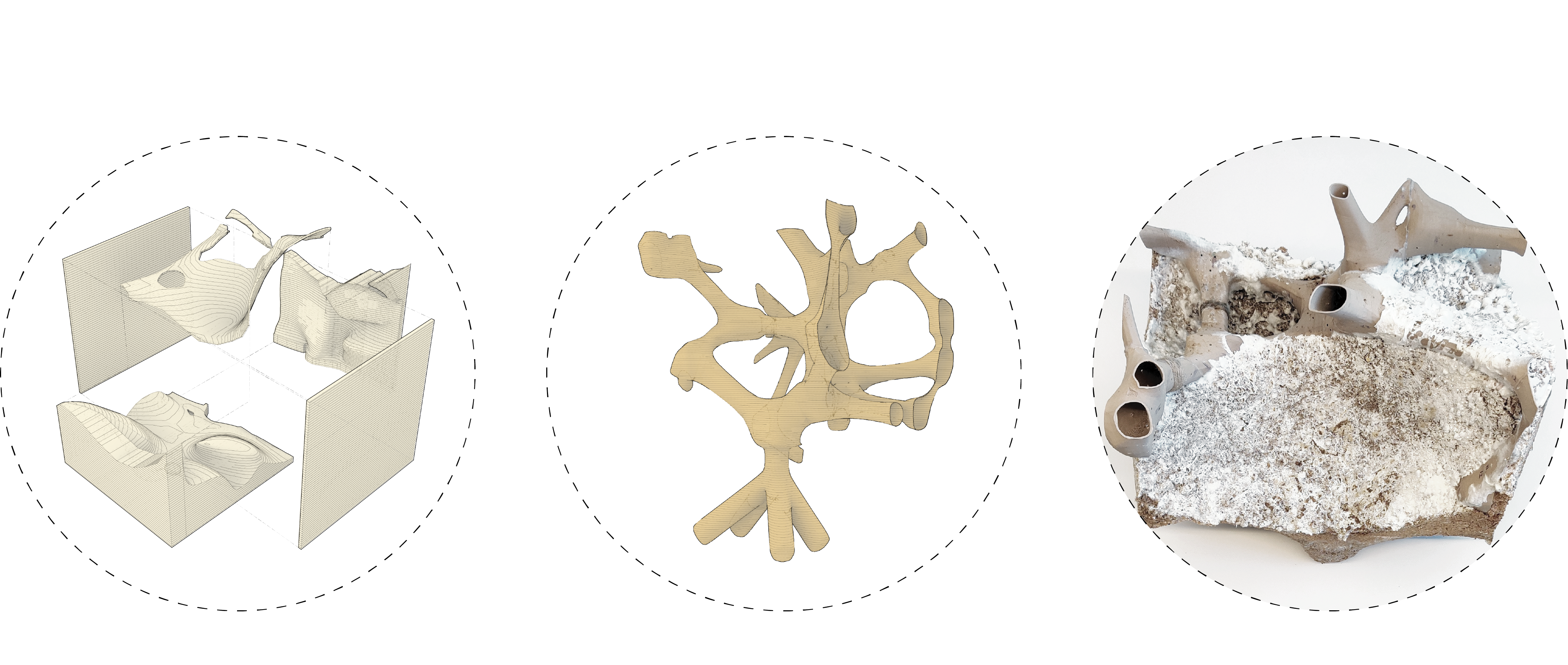
For testing the function of the Living Wall system, a chunk of the all was made at scale of 1 : 2. In this prototype cavities were chopped into printable size by Creality 3D ender-3 V2 printer (220x220x250 mm) and were glued later. To mimic semi-porous surface of cellulose 3D printed in big scale, small holes with 1 inch threshold were drilled on the cavities. To facilitate the process, instead of the 3D printing moulds, CNC EPS was made for casting. It was filled with oyster mycelium inoculated into two
different substrates; one for the core and another one for the finish surfaces and it grew for two weeks
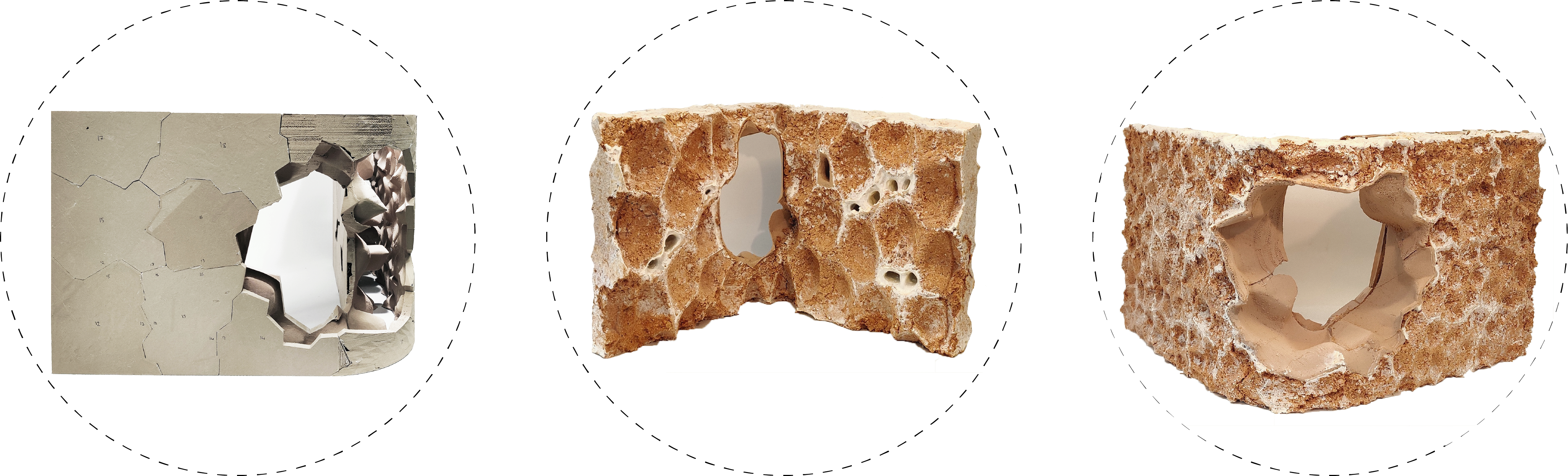
For testing fabrication and manufacturing technique of the Living Wall system whole L-corner was made at scale of 1 : 10. Two sets of exterior and interior, in addition to alcove surface moulds were 3D printed with light wooden PLA. After assembling pieces ,it was filled with oyster mycelium inoculated into straw and corn seed and it grew for two weeks.
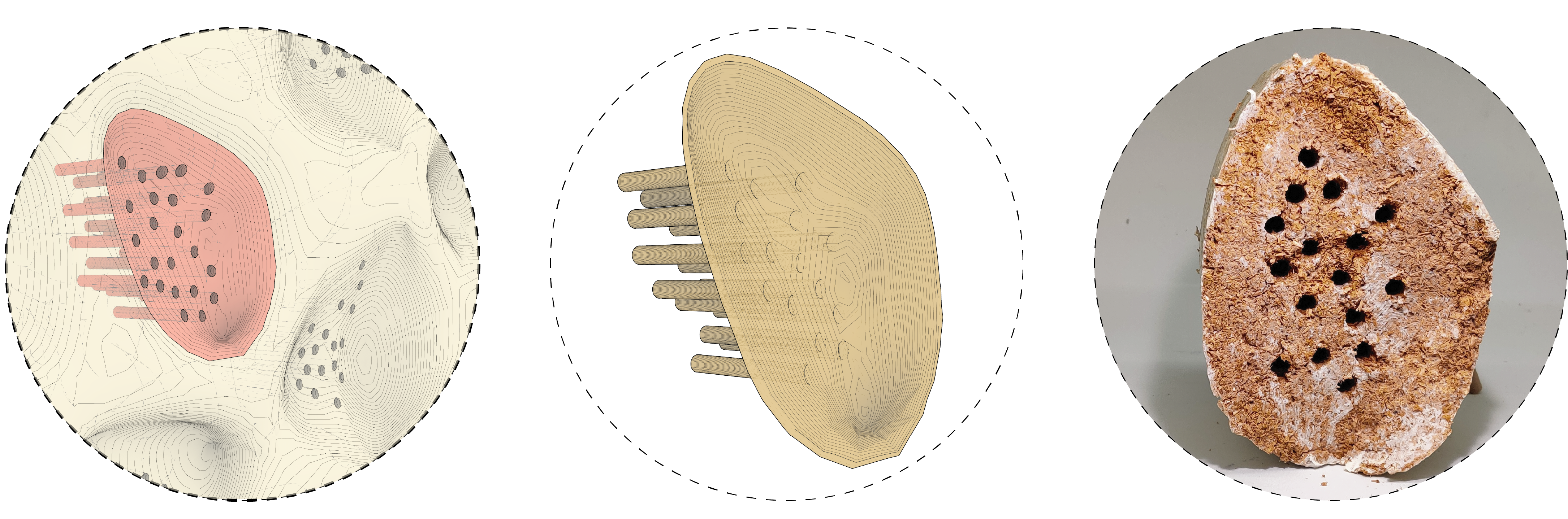
Cavity dwelling solitary bees require nesting tunnels of specific size and depth to reside. Prototype of the bee house was fabricated and grown with mycelium composite to understand the design specificity and surface quality for the suitability of the bee house.